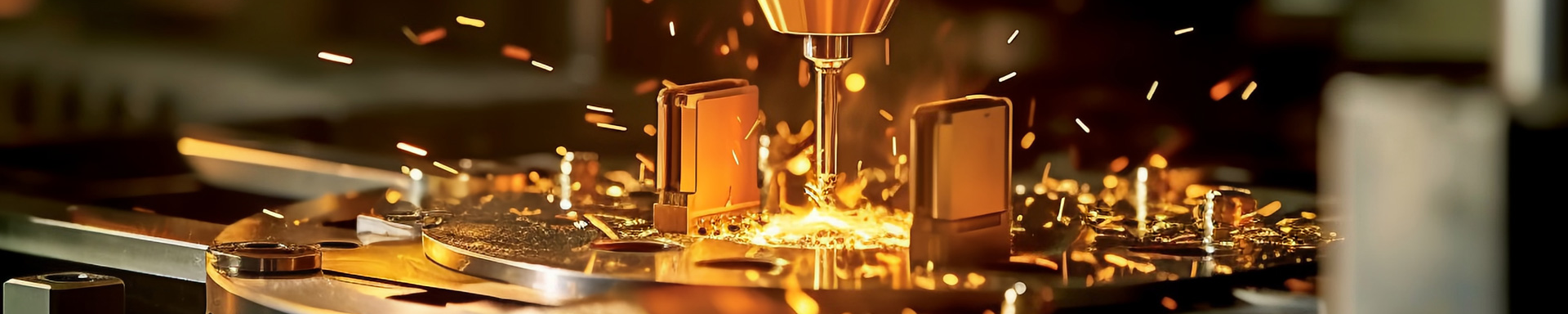
Hassas Kalıplama Enjeksiyonunun Dünyasını Keşfedin
2024-11-20 16:06Hassas kalıplama enjeksiyonunun dünyasını keşfedin, karmaşık tasarımların yüksek teknolojili makinelerle buluştuğu ve benzersiz doğruluk ve karmaşıklığa sahip parçalar yarattığı üretimin kalbine bir yolculuktur. Bir akıllı telefonun içindeki minik bileşenlerden bir arabanın sağlam yapısal elemanlarına kadar, hassas kalıplama enjeksiyonu modern dünyamızı şekillendirir. Bu süreci anlamak, mühendislik, malzeme bilimi ve üretim uzmanlığının büyüleyici bir etkileşimini ortaya çıkarır. Bu keşif, bu tekniğin karmaşıklıklarını araştırarak çeşitli endüstrilerdeki yeteneklerini ve uygulamalarını aydınlatır.
Hassas Kalıplama Enjeksiyonunun Temelleri
Enjeksiyon kalıplamanın bir alt kümesi olan hassas kalıplama enjeksiyonu, son derece sıkı toleranslara ve olağanüstü yüzey kaplamalarına sahip parçalar üretmeye odaklanır. Belirli bir boyutsal varyasyona izin veren standart enjeksiyon kalıplamanın aksine, hassas kalıplama, erimiş malzemenin sıcaklığından ve basıncından kalıbın kendisinin hassas hareketine kadar sürecin her yönü üzerinde kesin kontrol gerektirir. Bu, tüm üretim döngüsü boyunca gelişmiş makineler ve titiz izleme gerektirir. Sonuç, genellikle geleneksel üretim yöntemlerinin gereksinimlerini aşan, sıkı kalite standartlarını karşılayan bir bileşendir.
İşlemin özü, erimiş termoplastik veya termoset polimerin hassas bir şekilde tasarlanmış bir kalıp boşluğuna enjekte edilmesini içerir. Genellikle sertleştirilmiş çelikten veya diğer yüksek performanslı malzemelerden üretilen kalıp, istenen parçanın tam şeklini ve boyutlarını taklit edecek şekilde tasarlanmıştır. Erimiş plastik, yüksek basınç altında boşluğa zorlanır ve kalıbın her ayrıntısını doldurur. Plastik soğuduktan ve katılaştıktan sonra kalıp açılır ve bitmiş parça dışarı atılır. Tüm işlem son derece otomatiktir ve tutarlılık ve tekrarlanabilirlik sağlar.
Malzemeler ve Kalıp Tasarımı: Hassasiyetin Yapı Taşları
Malzeme seçimi hassasiyete ulaşmada kritik öneme sahiptir. Farklı polimerler, dayanıklılık, esneklik, ısı direnci ve kimyasal direnç gibi farklı özellikler sunar. Optimum malzemeyi seçmek, nihai ürünün amaçlanan uygulama gereksinimlerini karşılamasını sağlamada önemli bir adımdır. Bu seçim genellikle parçanın işlevi, çevre koşulları ve istenen kullanım ömrü gibi faktörleri göz önünde bulundurmayı içerir.
Kalıp tasarımı da aynı derecede önemli bir rol oynar. Hassas kalıplama, genellikle karmaşık özellikler, alt kesimler ve karmaşık geometriler içeren inanılmaz derecede sıkı toleranslara göre hazırlanmış kalıplar gerektirir. Bilgisayar destekli tasarım (CAD) ve bilgisayar destekli üretim (CAM), mühendislerin son derece ayrıntılı ve doğru kalıp tasarımları oluşturmasını sağlayan bu aşamada vazgeçilmez araçlardır. Gelişmiş yazılım, enjeksiyon sürecini simüle ederek kalıp tasarımını optimize etmeye ve üretim başlamadan önce olası sorunları tahmin etmeye yardımcı olur. Kalıbın kendisi için kullanılan malzeme, söz konusu yüksek basınçlara ve sıcaklıklara dayanacak kadar dayanıklı olmalı ve birçok döngü boyunca hassasiyeti korumak için gereken boyutsal kararlılığa sahip olmalıdır.
Kalite Kontrol ve Güvence: Mükemmelliğin Sağlanması
Hassas kalıplama enjeksiyonu, tüm süreç boyunca sıkı kalite kontrolü gerektirir. Her aşamada düzenli denetimler ve ölçümler yapılarak malzemelerin teknik özelliklere uygun olduğundan ve makinenin optimum şekilde çalıştığından emin olunur. İstatistiksel süreç kontrolü (SPC) teknikleri, süreç varyasyonlarını izlemek ve analiz etmek, bitmiş parçaların kalitesini etkilemeden önce olası sorunları belirlemek ve ele almak için kullanılır.
Koordinat ölçüm makineleri (CMM'ler) ve lazer tarayıcılar gibi gelişmiş ölçüm ekipmanları, kalıplanmış parçaların boyutlarını ve yüzey kalitesini doğrulamak için kullanılır. Bu araçlar, tasarım spesifikasyonlarından herhangi bir sapmanın kesin olarak belirlenmesine olanak tanıyan son derece hassas ölçümler sağlar. Ayrıca, X-ışını muayenesi gibi tahribatsız test yöntemleri, iç kusurları veya tutarsızlıkları tespit etmek için kullanılabilir. Kalite güvencesine yönelik bu titiz yaklaşım, hassas uygulamaların zorlu standartlarını karşılayan parçalar sunmak için olmazsa olmazdır.
Endüstriler Arası Uygulamalar: Geniş Bir Olasılık Yelpazesi
Hassas kalıplama enjeksiyonunun yetenekleri çok çeşitli endüstrilere yayılmıştır. Tıbbi cihaz endüstrisinde, implantlar, protezler ve teşhis araçları için karmaşık bileşenler oluşturmak için kullanılır ve olağanüstü doğruluk ve biyouyumluluk gerektirir. Otomotiv endüstrisi, yakıt enjeksiyon sistemleri, sensörler ve hassas boyutların ve toleransların optimum performans ve güvenlik için çok önemli olduğu diğer önemli parçalar için hassas kalıplama kullanır.
Elektronik üretimi, konektörlerin, muhafazaların ve diğer bileşenlerin oluşturulması için büyük ölçüde hassas kalıplamaya dayanır. Havacılık endüstrisi de bu teknolojiden yararlanarak uçak ve uzay araçları için hafif ancak dayanıklı parçalar üretir. Tüketim mallarında bile hassas kalıplama, elektronik, ev aletleri ve diğer ürünler için yüksek kaliteli, estetik açıdan hoş bileşenler oluşturmak için kullanılır. Bu üretim tekniğinin çok yönlülüğü ve hassasiyeti, onu etrafımızdaki dünyayı şekillendirmede vazgeçilmez bir araç haline getirir.
Hassas Kalıp Enjeksiyonunun Geleceği: Yenilik ve İlerleme
Hassas kalıplama enjeksiyonu alanı, malzeme bilimi, otomasyon ve üretim teknolojisindeki gelişmelerle yönlendirilerek sürekli olarak gelişmektedir. Geliştirilmiş özelliklere sahip yeni polimerler sürekli olarak geliştirilmekte ve bu tekniğin uygulama yelpazesi genişlemektedir. Robotik ve yapay zekanın (AI) entegrasyonu otomasyonu iyileştirerek artan verimliliğe ve iyileştirilmiş parça tutarlılığına yol açmaktadır.
Katkılı üretim teknikleri ayrıca geleneksel kalıplama süreçleriyle entegre ediliyor ve daha da karmaşık ve incelikli parçalar yaratma potansiyeli sunuyor. Teknoloji gelişmeye devam ettikçe, hassas kalıplama enjeksiyonu şüphesiz çeşitli endüstrilerde yüksek hassasiyetli bileşenlerin üretiminde giderek daha önemli bir rol oynayacak ve yenilikçi tasarım ve üretimin geleceğini şekillendirmeye devam edecektir.